The Art and Science Behind Engine Gasket Manufacturing: Unveiling the Masters of Seal
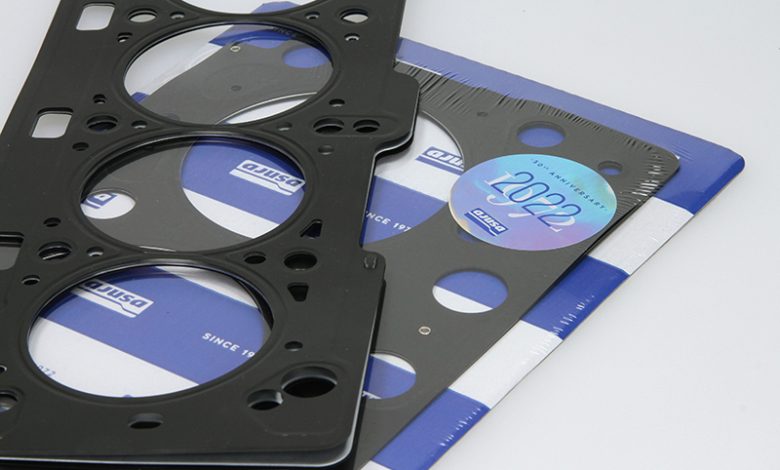
Introduction
In the intricate world of automotive engineering, where every component plays a vital role in the smooth functioning of an engine, engine gaskets stand out as unsung heroes. These small and inconspicuous pieces of material are instrumental in ensuring that an engine operates at its best efficiency by creating airtight seals between various components. Behind this critical component lies a complex and fascinating industry of engine gasket manufacturers, where precision, innovation, and attention to detail reign supreme.
The Role of Engine Gaskets
Engine gaskets serve a crucial purpose in internal combustion engines. They create seals between different engine components, preventing the leakage of fluids, gases, and combustion byproducts. These seals not only keep the engine running but also contribute to its performance, efficiency, and longevity. Gaskets used in various locations within an engine, such as between the cylinder head and engine block, intake and exhaust manifolds, and oil and coolant passages.
Materials and Technology
Manufacturing engine gaskets requires a deep understanding of materials and the application of advanced technologies. Gaskets made from materials like rubber, cork, paper, and metal. Each material has its own set of advantages and chosen based on the specific requirements of the engine and the conditions it operates under.
Rubber gaskets, for instance, known for their flexibility and ability to create effective seals in dynamic environments. Metal gaskets, but, favored for their durability and resistance to extreme temperatures. The choice of material depends on factors such as the operating temperature range, pressure, and the type of fluids the gasket will come in contact with.
In recent years, advancements in material science and manufacturing technologies have led to the development of composite gaskets that combine the best properties of different materials. These composite gaskets offer superior performance, improved durability, and enhanced resistance to a wide range of operating conditions.
Precision Manufacturing
Engine gasket manufacturing is a process that demands precision at every stage. The design and production of gaskets involve intricate measurements and specifications to ensure a perfect fit. Manufacturers use computer-aided design (CAD) software and sophisticated machinery to create precise molds and dies for gasket production.
Once the design finalized, the chosen material cut and shaped with extreme precision. Automated cutting systems and CNC (Computer Numerical Control) machines employed to achieve the required accuracy. This level of precision is essential to ensure that the gasket conforms to the shape and dimensions of the mating engine components.
Quality Control
The reliability of an engine gasket is paramount, and thus, stringent quality control measures implemented throughout the manufacturing process. Quality control starts with the inspection of raw materials to ensure that they meet the required standards. During production, gaskets inspected for dimensional accuracy, material consistency, and quality.
Advanced testing methods, such as leak testing, compression testing, and thermal testing, employed to verify the performance of the gaskets under simulated operating conditions. These tests help identify any defects or weaknesses in the gasket that could compromise its sealing capabilities.
Environmental Considerations
With an increasing emphasis on environmental sustainability, engine gasket manufacturers are also focusing on materials and manufacturing processes. The automotive industry as a whole is making strides towards reducing its environmental impact, and gasket manufacturers play a vital role in this effort.
Some manufacturers are exploring the use of recycled materials for gasket production, while others are developing gaskets that are more resistant to wear and must less frequent replacement. Additionally, efforts are being made to optimize manufacturing processes to cut waste and energy consumption.
Innovation in Design
As engines evolve with advancements in technology, engine gaskets must keep pace with new design requirements. Manufacturers are innovating to meet the challenges posed by modern engine designs, which often involve higher temperatures, increased pressures, and a variety of fuels and lubricants.
One area of innovation is the development of multi-layered steel (MLS) gaskets, whichdesigned to provide superior sealing performance in high-performance engines. MLS gaskets consist of many layers of steel with elastomer coatings, offering enhanced resilience and durability under extreme conditions.
Global Market Dynamics
The market for engine gaskets influenced by global trends in the automotive industry. The increasing demand for fuel-efficient and friendly vehicles has led to the development of advanced engine technologies, which, in turn, impact the requirements for engine gaskets.
The global distribution of engine gasket manufacturers reflects the geography of the automotive industry. Major automotive manufacturing hubs, such as Asia, Europe, and North America, house many of the world’s leading gasket manufacturers. These companies serve not only the original equipment manufacturer (OEM) market but also the aftermarket, providing replacement gaskets for vehicle maintenance and repairs.
Conclusion
Engine gaskets may be small in size, but their impact on the performance and reliability of internal combustion engines is immense. Behind the scenes, engine gasket manufacturers operate in a world of precision engineering, advanced materials, and constant innovation. As vehicles continue to evolve, so too will the demands on engine gaskets, driving manufacturers to push the boundaries of design and technology. In the dynamic and ever-changing landscape of automotive engineering, these masters of seal play a vital role in ensuring that engines run and with minimal environmental impact.